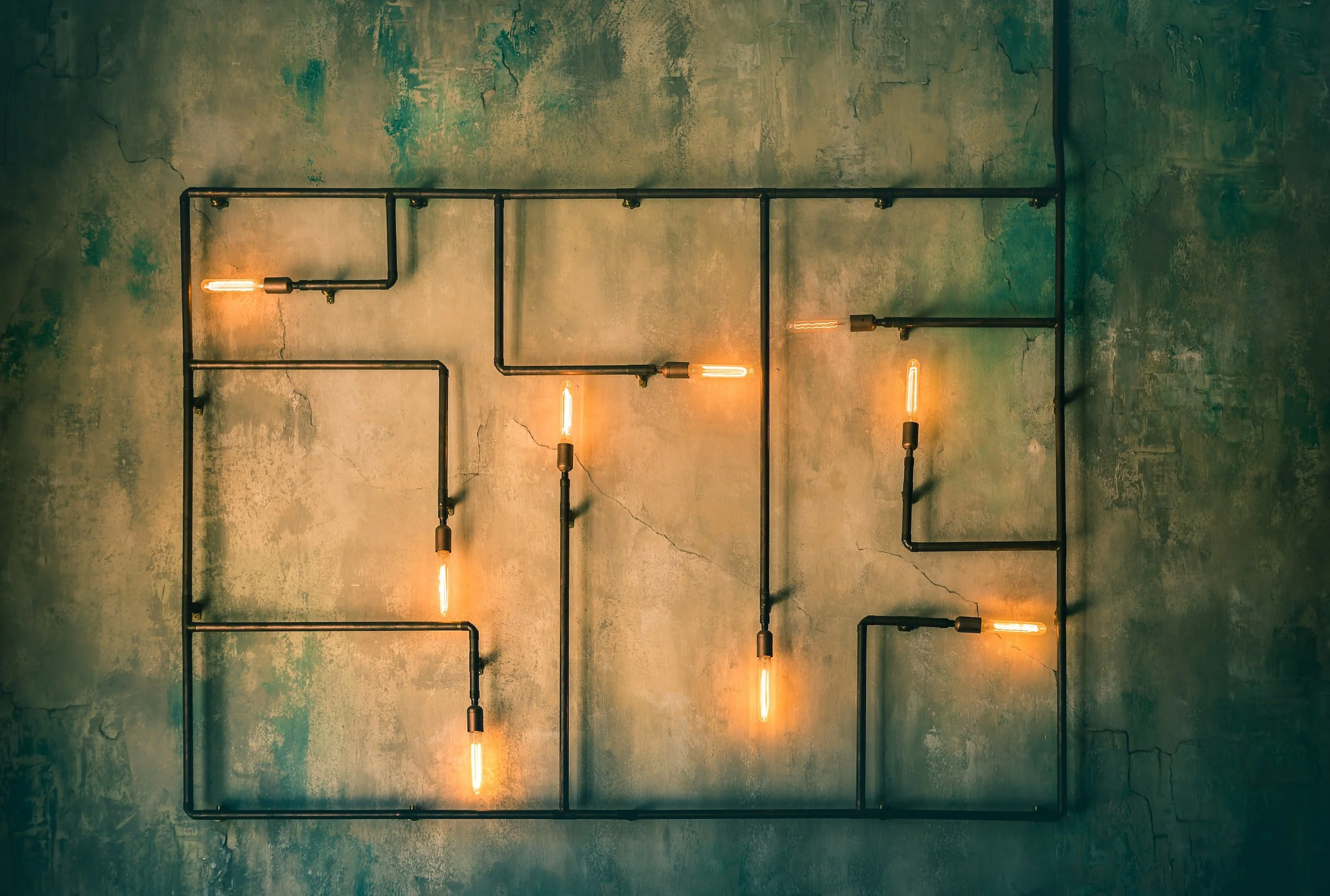
3 hats organizing
here to organize your space & improve your processes
We use proven engineering methodology to improve the layout, usage, and performance of your space. We have the background, experience, and vision to turn any disorganized area into a space you are proud of.
Our Services
-
INDUSTRIAL
Is your company experiencing strain from a lack of industrial engineering resources, or are you simply looking to improve overall process flow? Our industrial organizing services will meet your company at their place of need and implement processes to increase efficiency and ultimately improve your use of resources.
-
COMMERCIAL
Streamline the processes in your commercial space to create a work environment that promotes productivity for all of your team members. Whether you have a break room that needs a refresh, a stockroom that is in disarray, or desks that are buried under clutter, our proven processes can help!
-
RESIDENTIAL
Through developed processes such as color coding, space planning, and more, we will transform your space from a source of stress to a chaos free zone that you truly enjoy. We are skilled in organizing the toughest of pantries, home offices, man caves, garages, closets, and more!
meet the pro
Brad Boals
Owner and lead consultant, Brad Boals has over 20 years of experience in Industrial and Manufacturing Engineering. He has a Bachelor’s of Science Degree from the University of Tennessee at Martin and has participated and led hundreds of Industrial improvement projects.
3 Hats believes in the power of organizing, variable control, and proven industrial methods to help your business find improvement opportunities, save money, and improve your team’s morale. Those same methods can be used to help homeowners reach their goals to organize the spaces that are most important in their lives.
Are you ready to get organized?
We believe no two projects are the same, and our approach to each project varies in strategy based on your needs. We would love the chance to get together, assess your space, and create a game plan for bringing your organizational vision to life!
We Improve Efficiency and Cost
& We Have the Results to Prove It!